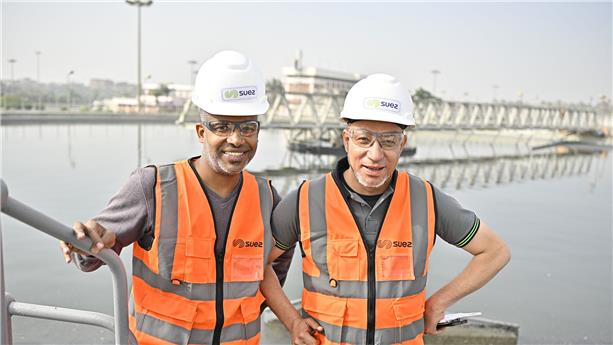
To treat sludge in two successive initial phases
Thickening and dewatering start the sludge treatment process in order to:
- Reduce the volume of the sludge
- Reduce the size of facilities and operating costs
- To optimally separate the water from the matter
Thickening is essential in order to reduce the volume of the sludge produced by wastewater treatment. It optimises the following conditioning, stabilisation and dewatering phases by reducing the size of facilities and equipment, and the operating costs. Dewatering improves efficiency and optimises operating costs.
Conditioning, which forms the basis of efficient dewatering, aims to artificially increase the size of the particles in order to improve separation and optimise the final dewatering content (*).
(*) the percentage of dry matter by weight
Implementing innovative thickening and dewatering processes
Static thickening, by gravitational settling
Static thickening calls on conventional and innovative techniques, such as Drainis Turbo that eliminates the water at speeds higher than the conventional speeds, thereby optimising the downstream dewatering phase (reduction of the amount of equipment, energy and reagent consumption, etc.).
Dynamic thickening, a concentration process that calls on dynamic energy
Dynamic thickening uses a complete range of different units that are selected to best meet the operating conditions of the process chosen by SUEZ.
After the thickening phase, dewatering uses different techniques that are selected to best meet the operating conditions of the process chosen by SUEZ.
Dehydris Lime for dewatering by pre-liming the sludge with centrifugation
This process can be used for dewatering all types of sludge produced by the treatment of wastewater in three steps:
1. pre-liming the decanted or thickened sludge,
2. conditioning with polymers,
3. dewatering by centrifugation.